
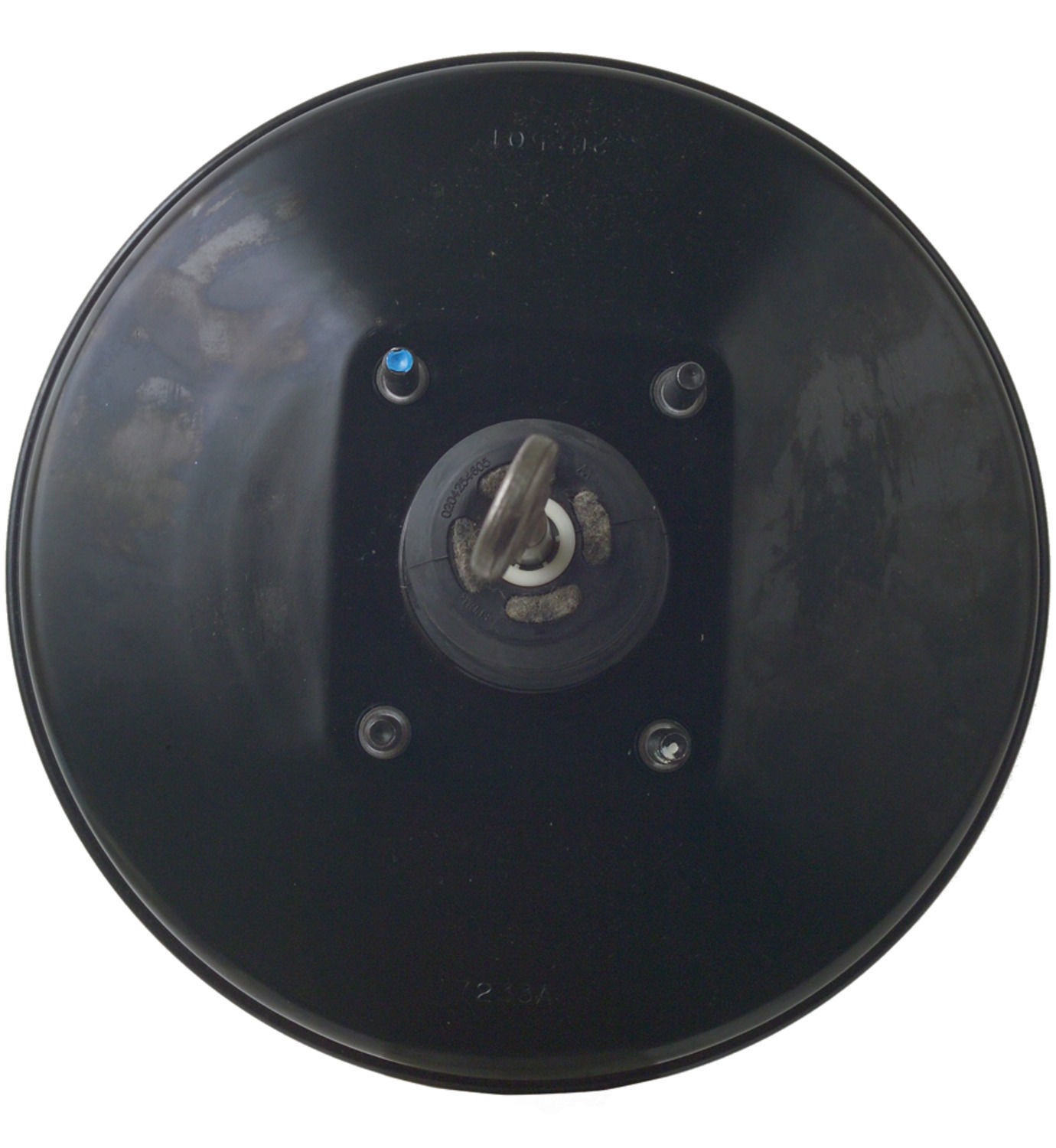
After a while our customers were telling us that the electric motors would burn out faster than they would expect and the units would fail.
#Power booster brake update#
The advantage of being in business for 60 years is that your customers update you on how products worked out, and you can adapt to improve. So Bob at Power Brake Service developed what is now being called the Electric Brake in the mid to late 80's, because it seemed to solve the lack of vacuum problems that the muscle cars and hot rods we normally see have, because of their blowers and huge cams. No vacuum + vacuum booster = fast car with no brakes. I have only driven my truck 20 miles before putting it in the shop for the winter (and to finish the bed).īut i can tell you that they work rather well.īoth of these units were used to try and work around the complete lack of vacuum that the two cars had because of the supercharging they came with. Thus lowering the pedal to the floor (remember those weak *** legs). but i was able to cut 3" out of the pedal height, I did not move the pivot points of the original swing arm. My truck has power steering anyway, picture above is before plumbing the hydro lines. I found a hydroboost out of an 03 mustang gt, junkyard purchased for $100.įabbed the bracket and made a plate to weld in my frame that the bracket would bolt to. hanging pedal with 12" vacume booster wouldn't work.įrame mounted 7" vacume booster didn't fit my needs (weak *** legs). I wanted power brakes and a shaved firewall. Project 58 chevy pickup: mustII front disc & 86 trans am rear disc brakes. I realize this thread was started in 05, but i thought i would put I had considered using the brake fluid pump from an ABS system as a power source because they are good quality but, decided not to chance using a motor /pump that was supposed to come on a few times a year for continuous use. The units are more expensive than power steering systems because they are constantly failing so the supply of rebuilds runs low and the supply of "cores" run low - driving the core charge through the roof.
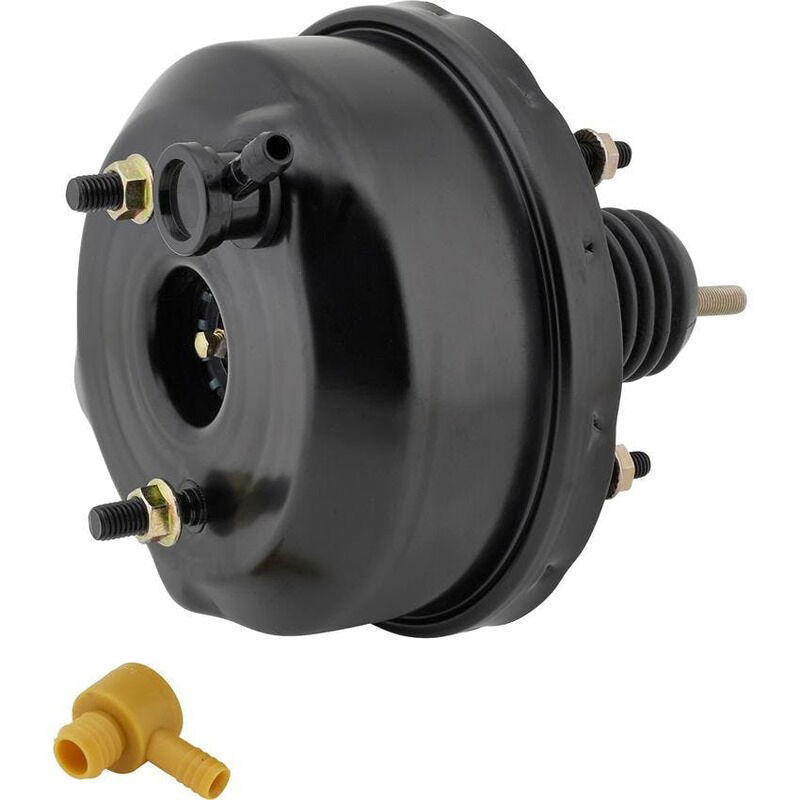
So far things are ok until: Something leaks, the cheap pressure switch contacts stick or don't make, fluid runs low and the system stays on until the motor smokes or the pump gets hot enough to melt the "o" ring seals. The pump motor would shut off until the pressure dropped back down (the brakes were pressed). How it was supposed to work: The pump would come on and pump fluid until a pressure switch was satisfied at 1200 psi. The pump would strain to reach the design pressure.

They were not careful with fluid connector choices, pump body was aluminum, etc. They chose to use a very cheap electric brush motor that is below the quality of say a electric window motor. The problem with the electric driven pump power source is that the pump design is below poor. Hydroboost itself is a fabulous mature design when it uses a power steering pump to supply the > 1000 psi fluid pressure as the boost power source. This is not something you would want to adapt into a project. It was used where there was cramped space under the hood in the normal area of the master cylinder.
